Taylor and I had ideas about building a kegerator to have beer on tap for our 23rd/25th birthday party this year. The party blew past us, and while we got two kegs, the kegerator did not make it. The following days after the party, we quickly found we needed to keep the remainder of the beer kegs cold, and ice is not cheap. First order of business, put the keg where it will stay cold without ice!
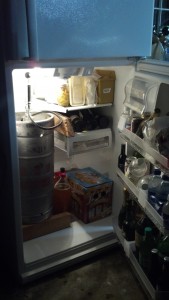
Good thing this is the second fridge, in the garage!
So there it sat until Black Friday, when Taylor happened across a chest freezer that happened to fall within our price range. During the previous week, all the CO2 tap and faucet parts came in mail, in anticipation of actually building a kegerator.
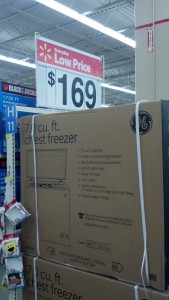
Chest freezer, on sale!
Building a Collar
When measuring the internal height available in the chest freezer, we found that the tapped keg was about an inch too tall for the freezer. Fortunately we have the option of building a collar, common practice for chest freezer based kegerators. This saves us from drilling into the actual freezer, because we can mount the beer faucets in the collar.
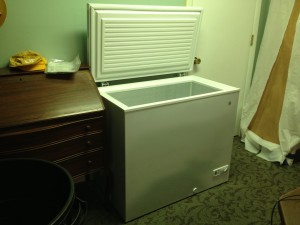
Chest freezer after unboxing at kegerator installation location
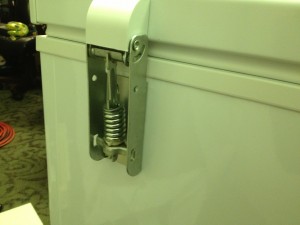
Original hinge installation, after removing the plastic cover
After doing some measuring and hinge investigation, we decided we needed to make a home depot run for supplies. While at HD, it occurred to us that we could buy the wood for both the frame and the trim of the collar, and get all the wood cut to size at HD. That way we would not need to cut anything once we got home. Taylor did some quick calculations and we tapped out all the cut lengths we would need into my phone.
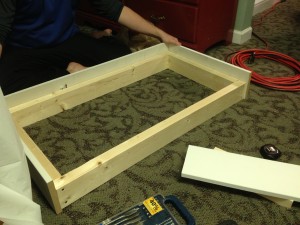
Test fitting the white outer trim pieces to the collar frame
We did save ourselves the trouble of cutting the wood, but the odd fractional inch sizes were accidentally swapped between the frame length and the trim lengths. No worries, the collar still fits left to right, and the trim hangs down over the front, but not the back of the freezer. You can see the inside of the collar in the above picture, where the collar is updside-down and while we test fit the trim pieces.
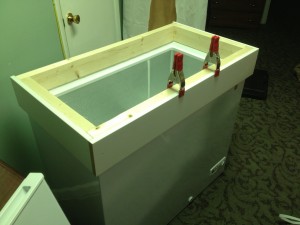
Clamping the trim to the collar frame while the liquid nails sets
Because the sizes were mixed up, you can see that the back of the collar is not properly flush with the freezer in the picture below. We decided to use washers to shim up the hinges, and will apply a shim and a retaining piece to the back later. The retaining piece will make the collar feel more stable because it will not slide forward like it can now.
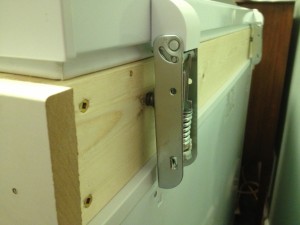
Lid hinge position, with washers to space it out from the collar frame appropriately
The lid actually would not close properly because of the incorrect dimension. Quick and easy fix: we used a 45 degree chamfer routing bit to take enough off the back 2×4 to make lid seat properly.
The Results
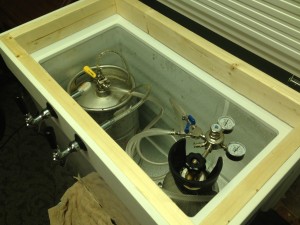
Faucets installed in the collar, and CO2 + Beer in the kegerator
With the collar finally in place and the faucets installed in the collar, its time to pull beer!
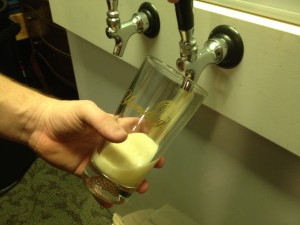
First glass of beer, pulled from the new kegerator
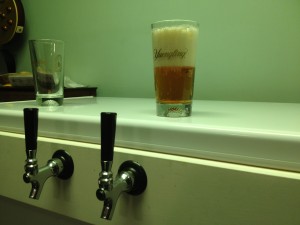
First pint drawn from the kegerator, after the pull
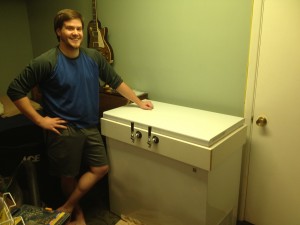
Taylor, a proud craftsman, posing with the fruit of our day’s labor
Future Improvements
- Add a shimmed retention piece to the back: this will make the collar feel a bit more stable because it will not be able to slide forward. Fortunately, the current feeling is already pretty stable.
- Hinge Bottom Plate: by adding a plate that bolts into the original hinge holes, we can ensure that the hinges are properly supported while the lid is being closed. Currently we just hold them while carefully closing the lid.
- Temperature Control: Right now, we just have it set to the warmest setting. Unfortunately, that freezes the beer. While the thermostat is still in the mail, we will be turning the freezer on a night, so the beer does not get too warm, and then leaving it off during the day so it will not be frozen when we want to pull beer.