Updated: March 11, 2011
Here is where additional info will be posted for project bedloft. Currently all info that I do have is in the below-pasted proposal and a dropbox folder of mine, which includes things like justifications for board calculations and what-not.
Files
Initial Hand Sketch
SolidWorks Generated BOM (not formatted wonderfully)
SolidWorks Model
Currently Unimplemented Features
Not Hand Drafted
-Plywood insert to allow bed in upper
-Side Attachment (bed-size)
–Built in bedside table
–Built in desk under attachment
–Hinge Down extension to accomodate a bed
—Hinged (to vert. supports) support for bed
-Hinged/Fold over cover to allow additional desk space
-Sway Bracing
Change
-Bottom Platform to be more low waste and compact
–No plywood, 2×4’s and 1×4’s for slats,
(two assemblies that mate)
–Not attached to rest of loft (has own legs),
but does mate with it (slats overhang 2×4’s of loft)
Pictures
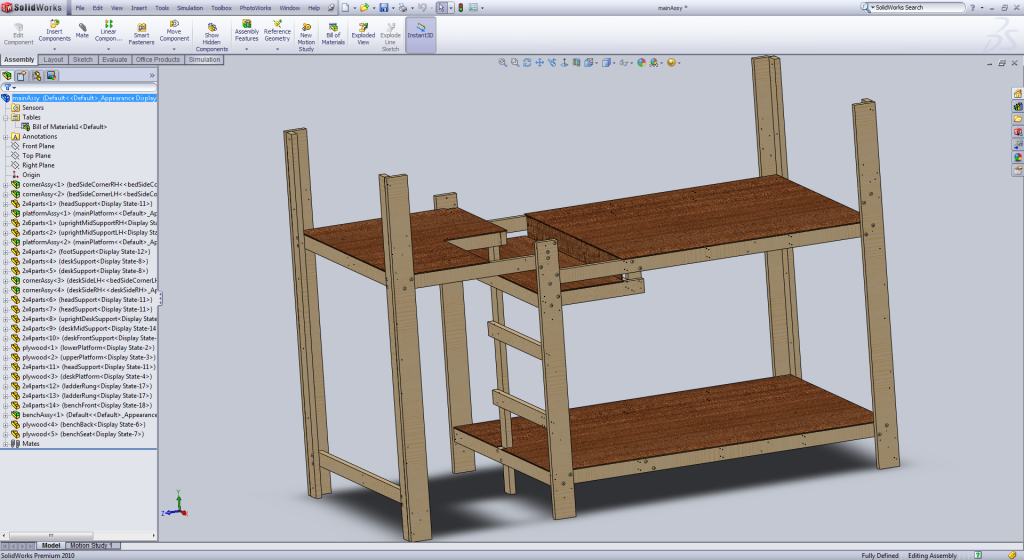
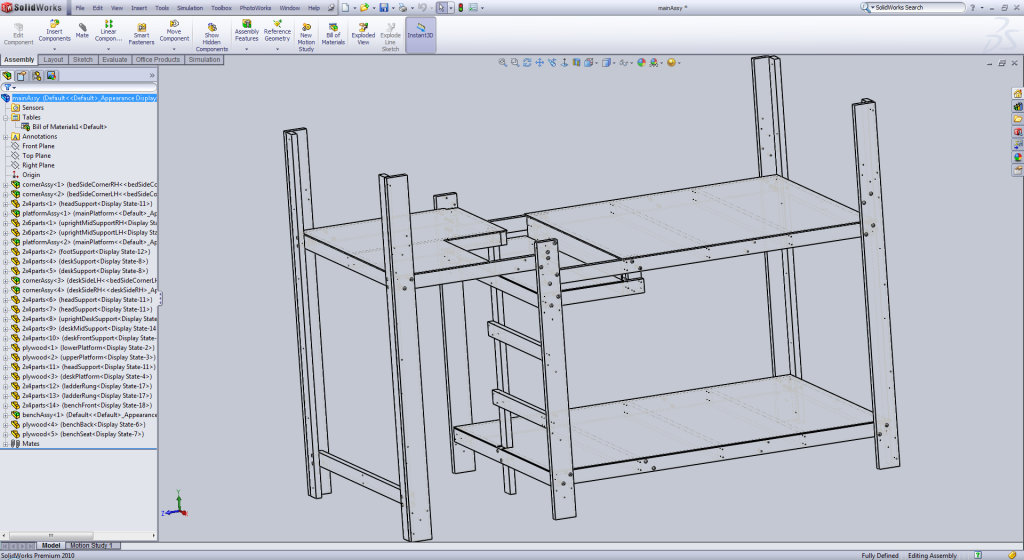
Seed Grant Proposal
Project BedLoft
What is It?
Project BedLoft is exactly that: a lofted bed that supports up to a queen size mattress. Other amenities that it has includes a desk space for two, and the option for the seat to be covered to make all the space on top storage space. Additionally there is space under the bed for small things to be stored.
Origin:
I conceived of this project to solve the problem of a cramped living space. Like most college students, I am mostly confined to one or two rooms wherever I am (currently I am off campus), and my room is generally stuffed full of my stuff. Building a way to utilize currently unused space would greatly help organize the room and lower stress levels (being stressed when things are overly messy).
Design and Considerations:
I designed this about a year ago, when I was in a different living situation (a coop apartment in South Carolina) that was very small. The bed size was chosen based on what mattresses I already had. The addition of the desk was something that I thought was cool, and would be a place where I could set up my computer(s) and be able to have them correct no matter what other furniture is available to me. In designing the desk, and the rest of the bed, there was a lot of visualization to get the right dimensions/proportions, and some searching online to find how professionals do things (like the height from the desk chair to the desk surface ~ 10 inches, by the way). Another feature of the bedloft is how easily it can be taken apart for storage or transportation. I designed it to break down into small pieces that were mostly flat such that it could be transported to and installed in a new place relatively easily. One would only need break it down and move the pieces, instead of try to finagle a huge mattress frame through hallways and doorways. The hardware holding it together is designed as lag bolts and t-nuts, which would make it easier to disassemble and reassemble, and most are designed to be the same type, so it is hard to use hardware in the wrong place.
Skills Needed:
The skills needed to build this project include a knowledge of SolidWorks for manipulating the current model to ensure it meets the requirements of my current living space, and to use as a template and guide for construction. Beyond that, I will need to be able to safely use a variety of power tools including (but not limited to) a miter saw, a table saw, and a drill press.
Bill of Materials:
Item |
Store |
Approx Unit Price |
Quantity |
Total |
2×4 lumber (stud) |
Home Depot |
$4
|
20
|
$80
|
2×6 lumber |
Home Depot |
$5
|
6
|
$30
|
4’x8′ Plywood |
Home Depot |
$25
|
3
|
$75
|
5/16th Lag Bolts |
Home Depot |
$40
|
1 (box 50)
|
$40
|
5/16th T-Nuts |
Home Depot |
$1
|
14 (4 pack)
|
$14
|
Forstner Bit
(if needed) |
Home Depot |
$11
|
1
|
$11
|
|
|
|
Total
|
$250
|
Goals and Scope:
This project could easily be done in less than a week, given all day every day to work on it. However, with my time constraints, coupled with finding a ULI to work in there with me, I would overestimate the project to take a month, which would be before the end of the semester. I would likely be able to take advantage of lab hours on most Tuesdays and Thursdays.
More Information:
More information is be available upon request, and may be available (if I have time to put it up…) at http://unrulyrecursion.com/press/2012/03/project-bedloft/