I recently had the opportunity to design (and have fabricated) a sheet metal chassis for my Fender 5E3 clone guitar amp. I was given a few hints about what things were possible with an industrial press brake, but until I watched the parts get fabricated, I had never actually seen a serious vertical press brake. I learned quite a bit about how a skilled brake operator can fabricate beautiful parts even when the designer was clueless or negligent.
The following renderings of the sheet metal parts show the ubiquitous amount of features incorporated into the two parts, which was necessary for the compactness of my overall design (remember, I’m trying to squeeze a full size 1×12 combo amp into a practice amp format).
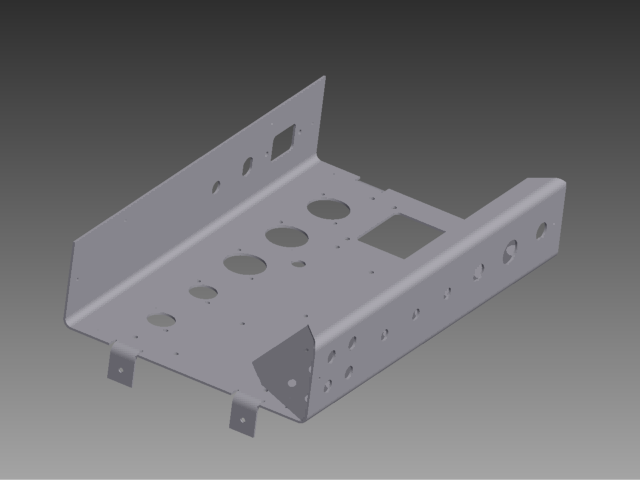
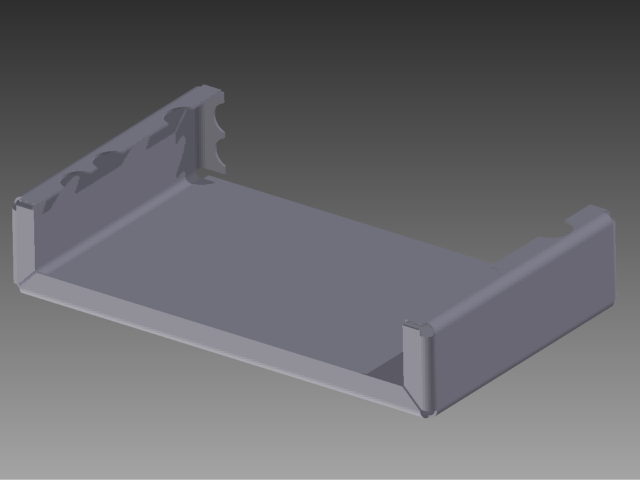
Many of these features are problematic, both when attempting to draw the feature, and when the brake operator was trying to bend the parts. Perhaps they are hard to draw, because programming the CAD tool to do something that is difficult to manufacture is not a priority!
The biggest issue with my design was features that were too close to the bend. Anything that is not perpendicular to the bend is subject to “roll out” according to the operator. He managed to beautifully bend several problematic flanges by using a “backing plate” technique. Not sure if that is an official term, but basically it amounts to bending the real part against the die, and having a support piece of sheet metal underneath it to make the weird features bend properly. You can see the difference between a normal bend and a backing plate bend by looking for the absence of the U-block tool mark, a slight discoloration line running parallel to the bend.
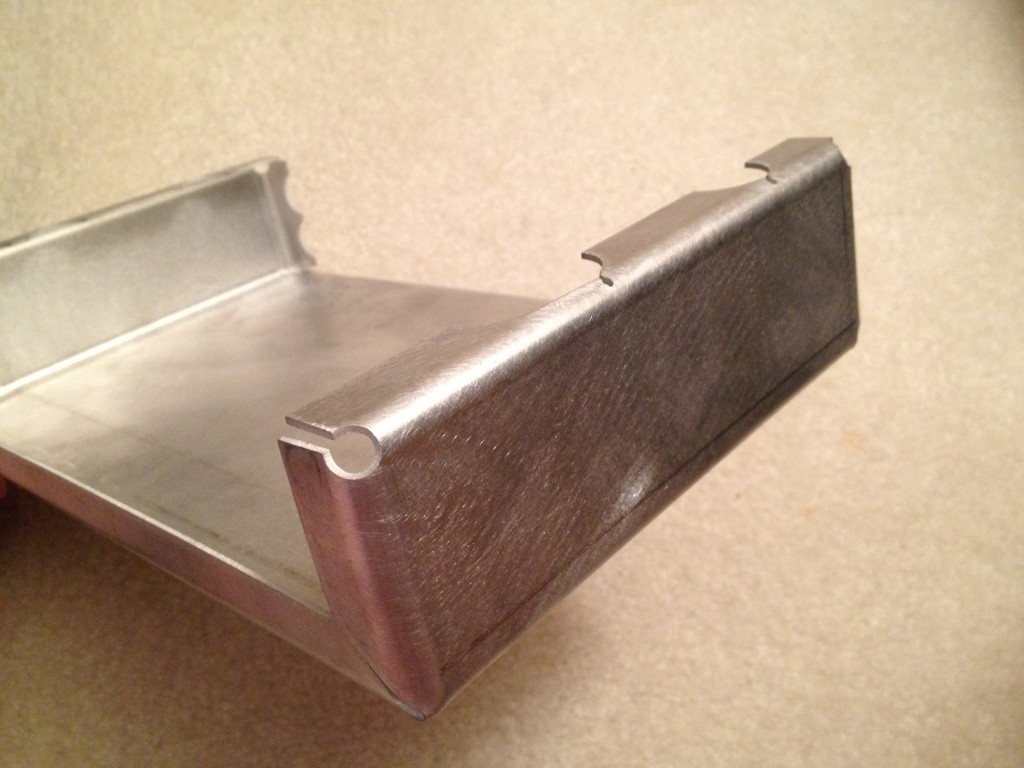
The two small holes in this part are defects from the water jet fabrication, not actual features in my model.
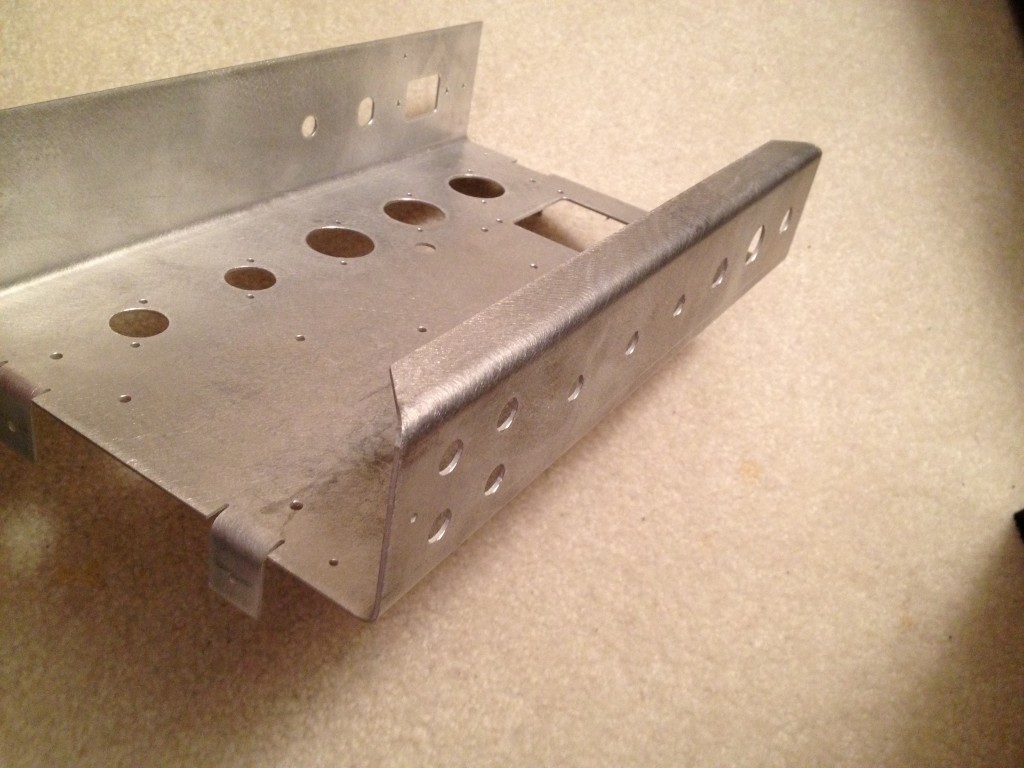
With this tooling mark, we can actually determine how to avoid the backing plate problem, which simplifies the fabrication of a one-off part considerably. The mark is .445 inches from the outside of the adjoining section, so the minimum safe bending flange length is .5 inches for my Aluminum 2024-T3 .062 thickness sheet at the minimum bend radius of 3/16″. Turns out, my 3/4″ flanges were a good safe length before cutting features out of them.
In the end, it took about two hours total to bend both parts, but it could have been twenty to thirty minutes if the flanges had been much simpler. I had been thinking that I wanted to the box to help shield circuit from RF noise as much as possible, but considering the old enclosure had negligible noise and negligible shielding the extra flanges are probably a waste.
Lessons Learned
- Avoid features that are not perpendicular to the bend near the bend radius. This includes angles, holes, circular cutouts, and other assorted odd features. These features actually are permissible, but should really be machined into the flanges after bending if at all possible.
- Make sure your flange lengths are long enough for the press brake to operate on them without a backing plate. This may be a guess in many cases, but a conservative guess is better than nothing.
- Use the minimum bend radius for the material you are using, unless there is a specific need otherwise. Many less skilled operators will ignore the drawing and default to the minimum bend radius chart for bending their parts.
- Call out every bend radius on your drawing. Do not leave these as a default, you might forget what you designed, or the operator may have to try and read your mind. If the operator uses the wrong die, your part will not come out the correct size and shape!
- Call out every flange length length and wall size on your drawing directly. Use reference dimensions if this involves over-dimensioning the part. (Hmm, can you guess why I decided that was a good idea? Do you really want the brake operator to be doing math in order figure out to bend your part?) Forget about your high school drafting class exercises, nobody wants spend time doing that in industry, and it makes the fabricator mad at the designer for ignoring his needs.
- Call out as many permutations of dimension on your flat pattern as you can think of, even if many of them are reference only. (Same thoughts as the previous bullet!)
- Avoid designing so many flanges that you have flanges meeting at a corner. It is really not a big deal when you are getting a large number of the part fabricated because the brake operator can justify cutting a die to the appropriate length. Unfortunately, this is typically cost prohibitive for one-off jobs. I got lucky because the brake operator had some appropriate custom dies laying around from other volume jobs recently run in the shop.
One additional item worth mentioning: machine calibration is rarely perfect. My brake operator was able to bend my parts with almost extreme precision, but he had to set up each type of bend with 3 or 4 test attempts before attempting to brake the actual part. If the machine readout was perfect, then he could have just punched in the numbers and bent the part. The operator had experience with the machine, and knew not to trust the readout without testing it, so my parts were not ruined, but that is why you should put as many dimensions on the flat pattern and folded views as possible. You really do not want to force the brake operator to be guessing or doing math on your part, that is what engineering is for!
I know I mentioned this before, but I really cannot stress it enough, DIMENSION EVERYTHING! Most machinists or machine operators did not make quite the grades you did in their math classes, and even if they did, you are trusting someone else to figure out something that you already know. Don’t be stingy, just tell them and you will get your parts back faster and cheaper!
NOTE: In my case, the parts I designed were being fabricated on a press brake, using the air bending technique illustrated in the video and the bottom image on that wikipedia page. If you believe wikipedia, the Sheet Metal page has some additional info, indicating that the bend radius is a function of the width of the lower U-block, V-block, or Y-block, but my inner radius was 3/16″ and die radius used in the brake was also 3/16″.